Standardised processes are the final step to freedom
John Nelligan
15-08-19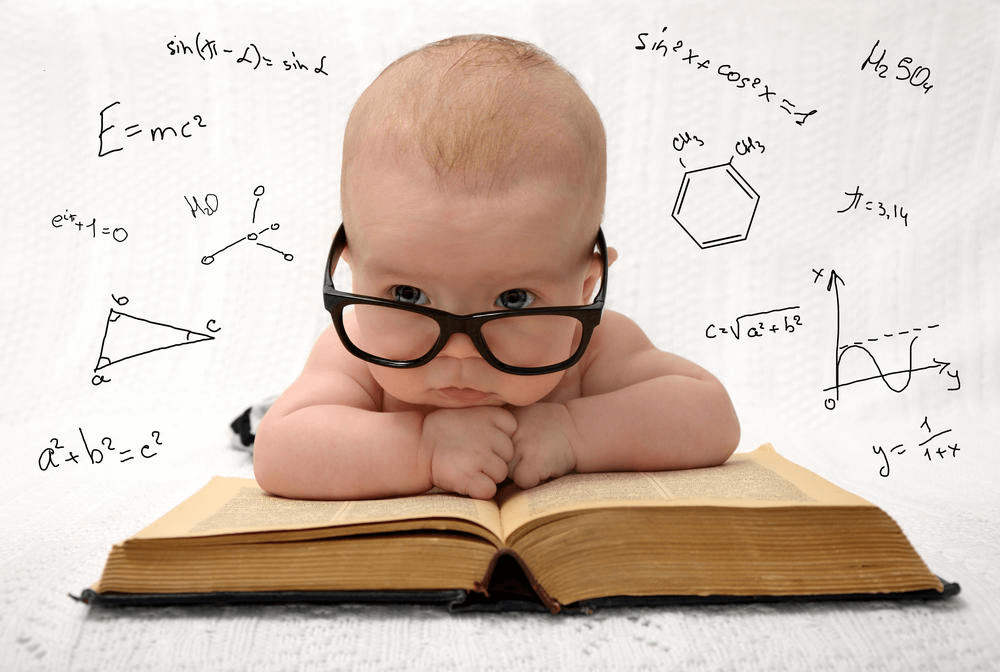
Having gone through a change management process and all of the associated pain and challenges, imagine how soul-destroying it would be to see that making changes has made no significant change in the figures a year later. And on investigation, we find things are being done the same way as before! Standardised processes and training for employees is the key to making sure changes stick.
Employees are key
This is not an uncommon scenario. We all work hard to involve our employees in creating the change, to get buy in from all of them. It creates a tremendous buzz at the time, but we later fall in to the same rut. It would be easy to blame the employees for this, but it is not them to blame.
If you leave employees without the direction or mechanism to be able to capture and retain the lessons, you are not giving them freedom to innovate – you are abandoning them to fate.
Brian Joiner in his book ‘4th Generation Management’ describes how a company in this situation has an ‘eyelash’ learning curve. Employees and staff develop technical skills and learn lessons from their work, but as soon as they leave or move on, all of that knowledge goes with them. Then the next person has to start from scratch. That creates a set of knowledge curves like the ones below.
Continuous learning
Now consider what will happen if there is are standardised processes for learning. Capturing knowledge and experience and recording for use by employees. Then there is a proper process for handing on knowledge before anyone moves on fearning rom a position. Instead of a series of curves like eyelashes, we get a cactus-shaped curve of knowledge as shown below. There is a consistent improvement, as each employee builds on the existing knowledge in the company.
Care needs to be taken however, that the process improvement does not stop. Firstly, this is not simply a mechanism to hand over institutional knowledge to new workers. It is also the mechanism to undertake effective training sessions. Skills fade and habits (good and bad) creep in.
Why have standardised processes?
- The world changes and technology changes. Best practice changes too. Having a way of recognising when things have to change or be updated.
- Often, procedures develop to overcome frictions created by flaws in the process. If this is codified, it reinforces the flaws into the process. By asking why we do things, we can identify where improvements can be made.
- We reduce the variation in how people are taught. When an employee teaches their successor their job, the variance gets ever bigger, just as a carpenter who cuts wood from the last piece he cut, rather than from the template, will end up with different lengths. There is a standard base of knowledge to make improvements from.
- Ensuring consistant behaviour will reduce the chance of blaming people for variations in performance, that are outside of their control. We will be able to stop putting in place reward and punishment schemes that do nothing but confuse and upset people.
- Finally, we can develop an effective and recognised mechanism for learning lessons or gaining knowledge. Embedding this into the company in a measurable and controlled manner creates a learning organisation rather than a collection of learning people.
More information
Wherever you are in your business journey, i can help provide business advice and support.
To find out more information about me or if you’re ready to find out how your business is feeling, book in a free business health check here.
Business Management
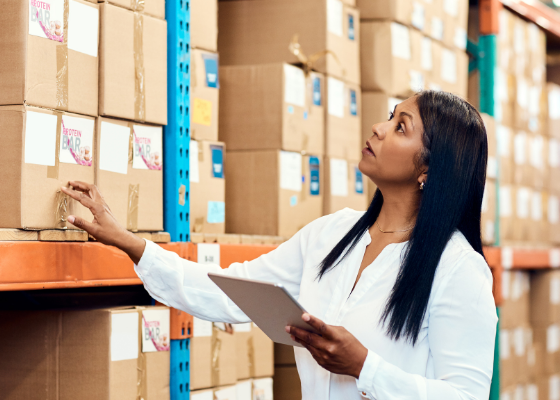
Business Management
How you manage your stock will depend on your business model, the type of stock your business uses, how much you...
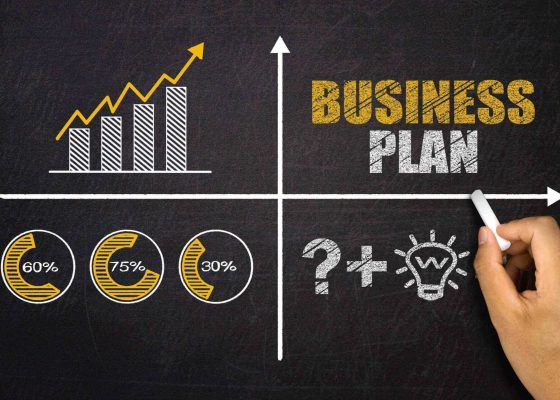
Business Management
Strategy
Strategy is important in business, right? It forms the foundation of all that we, as business owners, build our enterprises...
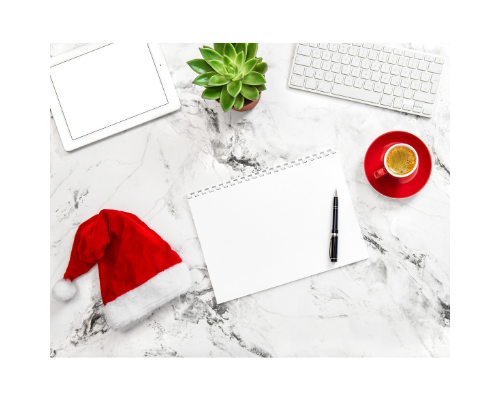
Business Management
With yuletide almost upon us, how can an SME ensure they properly prepare for the holiday close-down?